





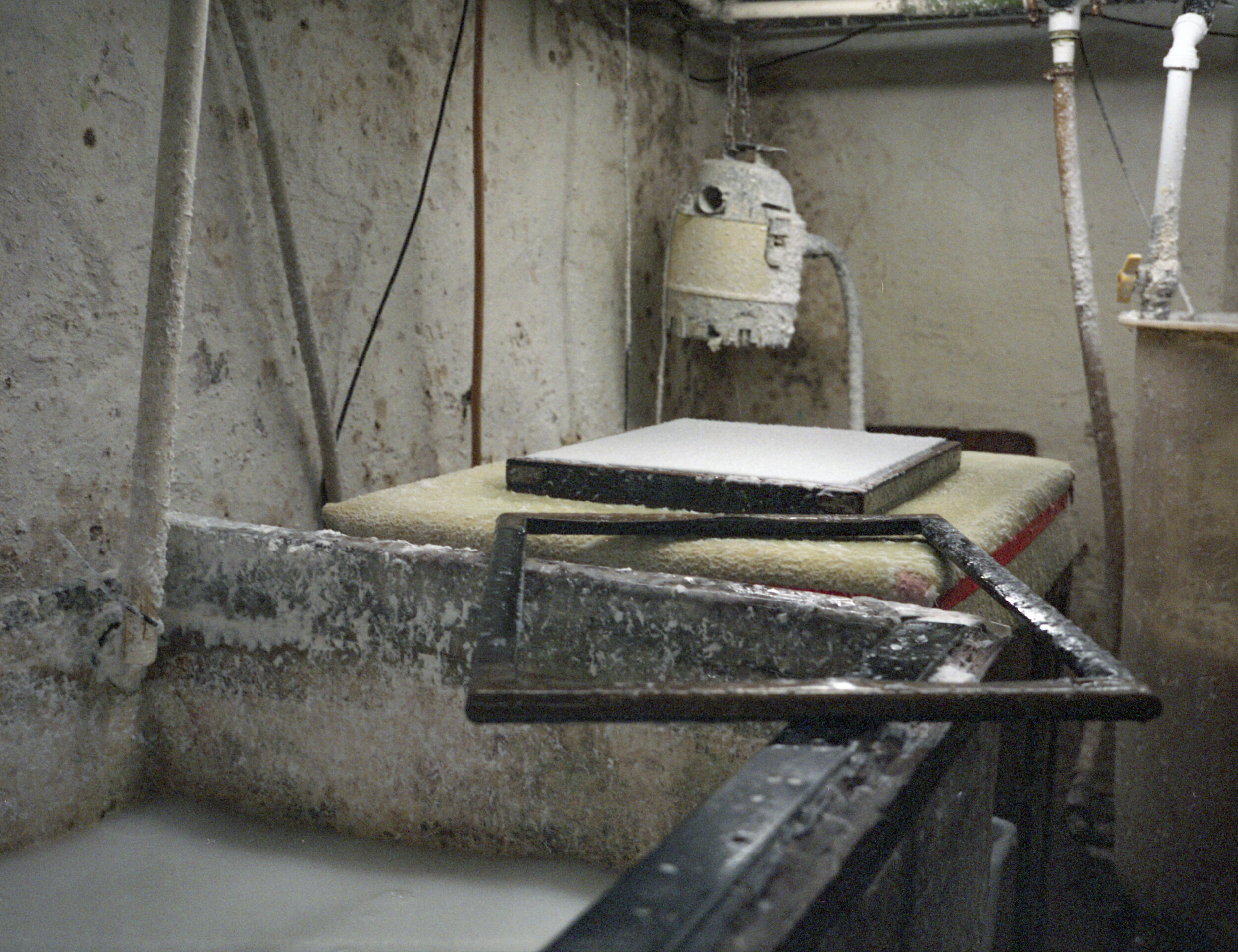





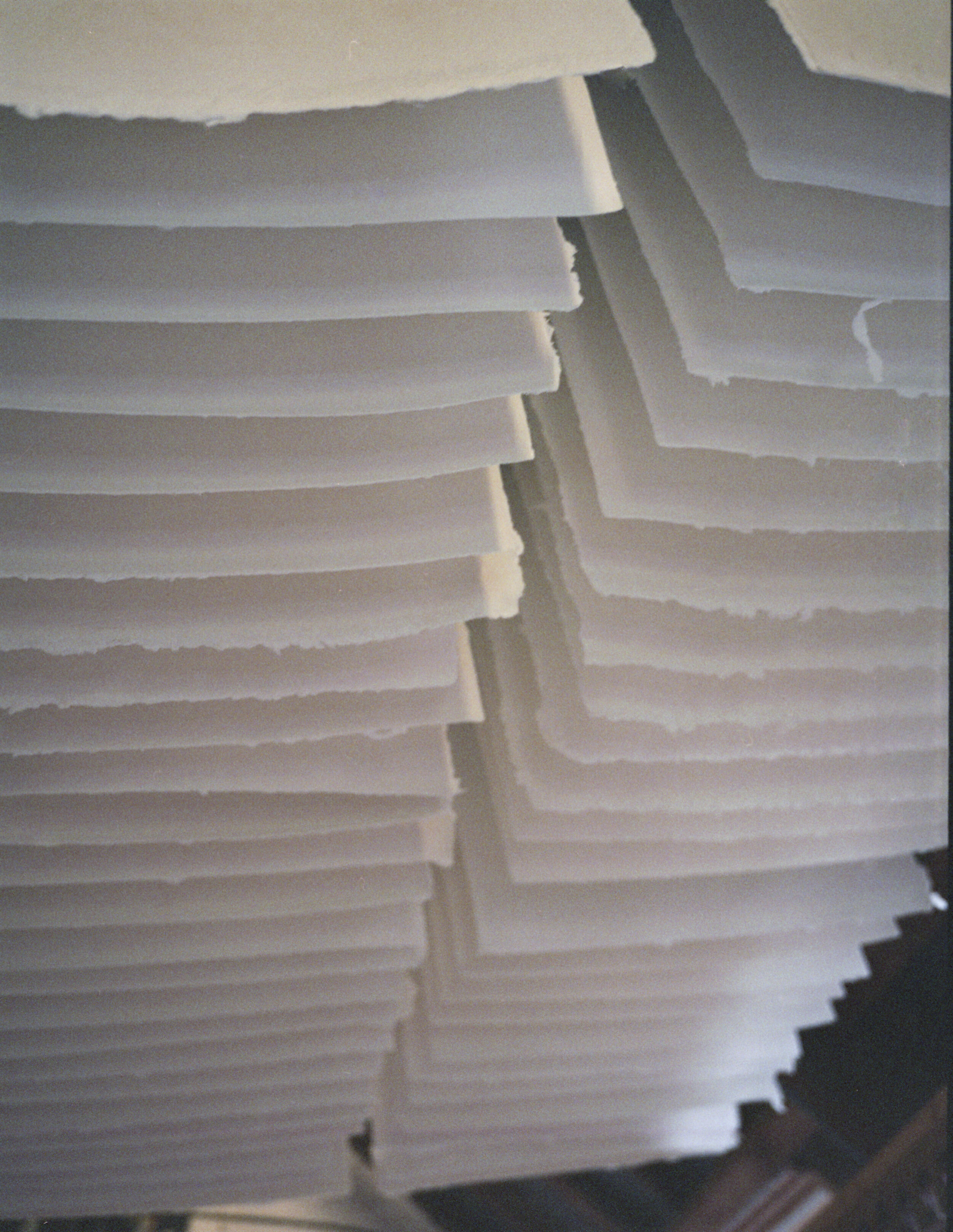


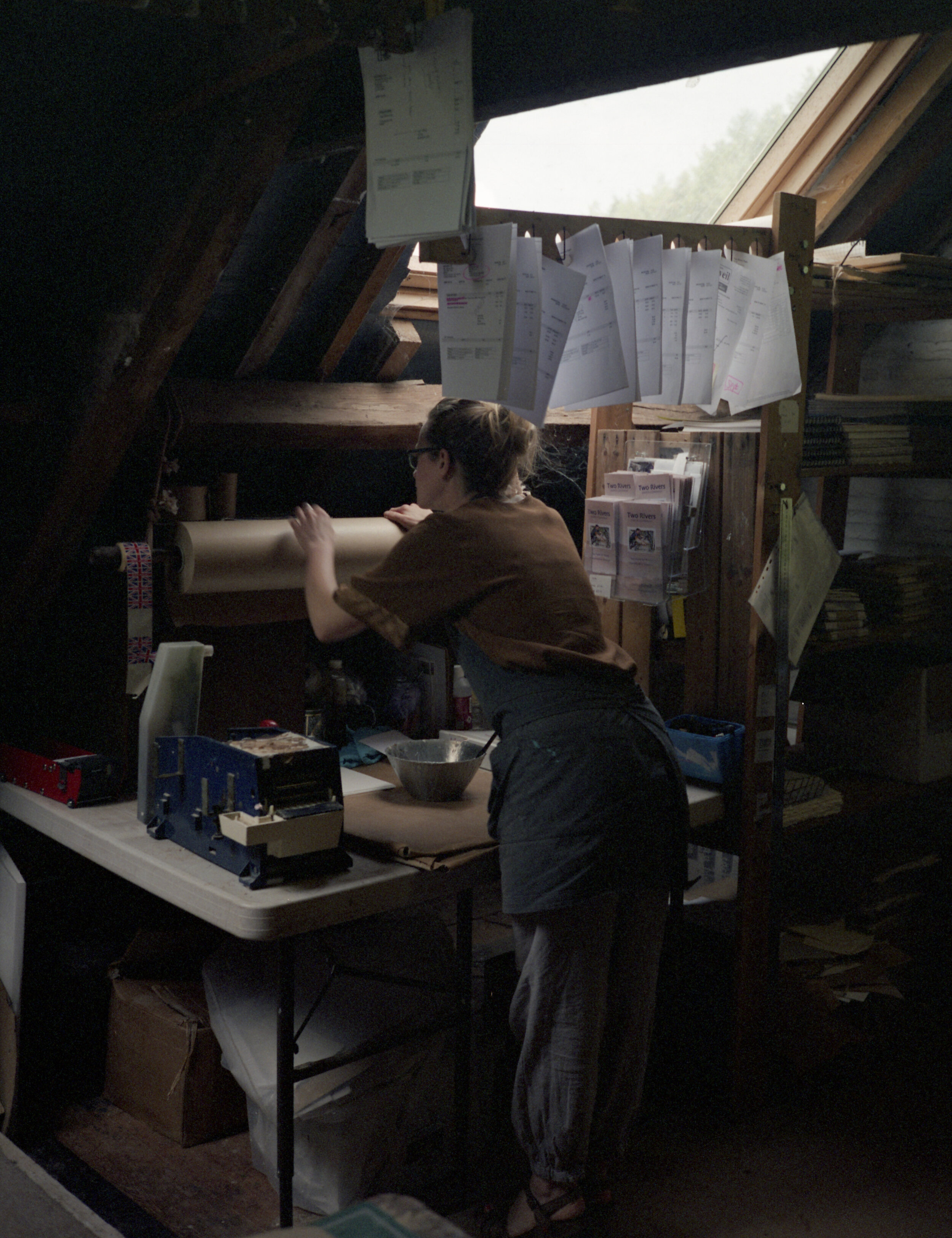


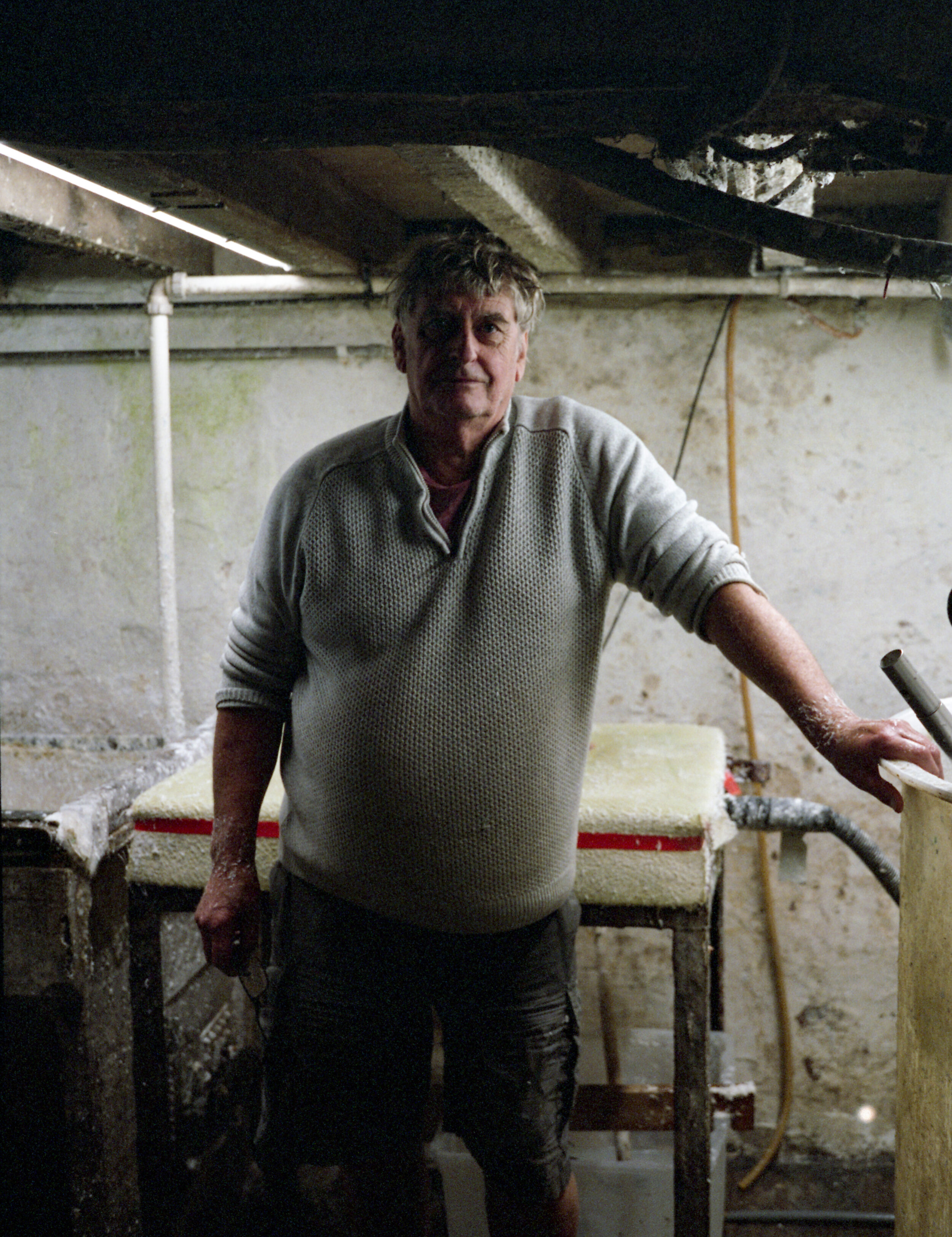
Your Custom Text Here
Two Rivers Paper Company, Pitt Mill, West Somerset
The four hundred plus year old Watermill that powers the machinery at Two Rivers Watermill is fed by the combining of two streams close to their source, that feed into the Washford River, before it flows into Bristol Channel at Watchet Marina. Ever since it opened as a paper-mill in 1988, the two and a half tonne, ten-foot wheel has been used to break down rags into their fibres to be used in the base of artist paper-stocks.
The team of five led by Jim Patterson produce a couple of thousand sheets of paper a week; mainly for sale online through art shops across the country of both paper, and hand bound books; but also for special assignments such as an upcoming commission with a distillery in Scotland wanting handmade labels for a special run of whiskies.
Jim has worked in various paper mills across the country and since starting Two Rivers Paper; and has spent time restarting production at working museums elsewhere in the country. He is supported by Neil, who on my visit was working in the loft of the mill and was drying paper, and packing orders for shipment; Sarah works in the bindery and manages the online orders. Kieran and Zoe both help in the production in both the main mill and the secondary smaller vat room set up in an outhouse a hundred meters up stream.
As much of the power to the mill as possible is gained through sustainable sources: the waterwheel that powers the mid nineteenth century Rag Breaker, and a large quantity of solar panels across the mill’s roof to help feed into the electrical needs of the mill’s hide glue vats, drying racks and paper presses. This focus on sustainability is matched by intentions to move most of the business away from the mill and to the tourist attraction of Watchet Marina in the coming years, as efforts to ensure that the business is future-proof, even if the working watermill perhaps is not.
The process starts on the ground floor of the mill, a wet environment with algae growing on the walls wherever they are not caked in layers of unrefined papier-mâché. Here the rag is crushed by the torque of the waterwheel, and added to a water tank. Stirred up with an oar the sediment is caught on a Deckle (a metal and wood screen), and then placed on a vacuumed bed. Here a paper plastered vacuum cleaner hangs from the ceiling and is used to draw the water out of the paper and condense its thickness to half, and by this process doubling the density of the paper.
The sheet is then transferred to a felt – a woven mat and stacked in a press where more the rest of the water is removed. The paper is then taken up two floors to the mill’s loft, and dried in a drying rack designed by Sarah Ward; one of Jim’s team at the Mill where it warmer. Once dry, it is taken back to the ground floor, and coated by being submerged in a vat of hide glue; a glue that is very similar to the glue used by musical instrument makers in wood joins. This paper is dried again in the loft, this time suspended from homemade marble racks before being packed up for sale or used at the mill in the production of both spiral-bound, and the more expensive hand bound sketchbooks.
This is a process that sees A1 sized paper made in batches of twenty to thirty sheets at a time, during the drying process of one batch, the start of another batch, or the glue coating of another is undertaken.
The location of the mill in the valley, so far from the local villages has a quiet romance to it. When I spoke with Jim about the paper they make here and the reason for doing so, I was expecting a romanticised or poetic response so in fitting with the location. The response though was far more keeping with his practical nature. The use of modern paper machines is far more consistent and practical than what they do, and more cost effective to maintain. However, there is a market for handmade paper for artists, and a need of the strength of the watermill’s wheel to tear down the rag for the paper stock. For Jim, much like most of the craft communities of the world, it is a job, and a satisfying one. This is the singular fact that separates the craft from the realm of the hobbyist.
Two Rivers Paper Company, Pitt Mill, West Somerset
The four hundred plus year old Watermill that powers the machinery at Two Rivers Watermill is fed by the combining of two streams close to their source, that feed into the Washford River, before it flows into Bristol Channel at Watchet Marina. Ever since it opened as a paper-mill in 1988, the two and a half tonne, ten-foot wheel has been used to break down rags into their fibres to be used in the base of artist paper-stocks.
The team of five led by Jim Patterson produce a couple of thousand sheets of paper a week; mainly for sale online through art shops across the country of both paper, and hand bound books; but also for special assignments such as an upcoming commission with a distillery in Scotland wanting handmade labels for a special run of whiskies.
Jim has worked in various paper mills across the country and since starting Two Rivers Paper; and has spent time restarting production at working museums elsewhere in the country. He is supported by Neil, who on my visit was working in the loft of the mill and was drying paper, and packing orders for shipment; Sarah works in the bindery and manages the online orders. Kieran and Zoe both help in the production in both the main mill and the secondary smaller vat room set up in an outhouse a hundred meters up stream.
As much of the power to the mill as possible is gained through sustainable sources: the waterwheel that powers the mid nineteenth century Rag Breaker, and a large quantity of solar panels across the mill’s roof to help feed into the electrical needs of the mill’s hide glue vats, drying racks and paper presses. This focus on sustainability is matched by intentions to move most of the business away from the mill and to the tourist attraction of Watchet Marina in the coming years, as efforts to ensure that the business is future-proof, even if the working watermill perhaps is not.
The process starts on the ground floor of the mill, a wet environment with algae growing on the walls wherever they are not caked in layers of unrefined papier-mâché. Here the rag is crushed by the torque of the waterwheel, and added to a water tank. Stirred up with an oar the sediment is caught on a Deckle (a metal and wood screen), and then placed on a vacuumed bed. Here a paper plastered vacuum cleaner hangs from the ceiling and is used to draw the water out of the paper and condense its thickness to half, and by this process doubling the density of the paper.
The sheet is then transferred to a felt – a woven mat and stacked in a press where more the rest of the water is removed. The paper is then taken up two floors to the mill’s loft, and dried in a drying rack designed by Sarah Ward; one of Jim’s team at the Mill where it warmer. Once dry, it is taken back to the ground floor, and coated by being submerged in a vat of hide glue; a glue that is very similar to the glue used by musical instrument makers in wood joins. This paper is dried again in the loft, this time suspended from homemade marble racks before being packed up for sale or used at the mill in the production of both spiral-bound, and the more expensive hand bound sketchbooks.
This is a process that sees A1 sized paper made in batches of twenty to thirty sheets at a time, during the drying process of one batch, the start of another batch, or the glue coating of another is undertaken.
The location of the mill in the valley, so far from the local villages has a quiet romance to it. When I spoke with Jim about the paper they make here and the reason for doing so, I was expecting a romanticised or poetic response so in fitting with the location. The response though was far more keeping with his practical nature. The use of modern paper machines is far more consistent and practical than what they do, and more cost effective to maintain. However, there is a market for handmade paper for artists, and a need of the strength of the watermill’s wheel to tear down the rag for the paper stock. For Jim, much like most of the craft communities of the world, it is a job, and a satisfying one. This is the singular fact that separates the craft from the realm of the hobbyist.
©Tom Warland 2024